Automotive rubber seals are used to prevent the ingress of water, dust, and other contaminants into the interior of vehicles. They are typically made from a variety of rubber materials, including EPDM, neoprene, and silicone, and are designed to provide a tight seal between the vehicle body and various components, such as windows, doors, and hoods.
Common types of automotive rubber seals include:
Door seals: These seals are used to provide a tight seal around the perimeter of the doors to prevent water, dust, and noise from entering the vehicle interior.
Window seals: These seals are used to provide a tight seal around the perimeter of the windows to prevent water, dust, and noise from entering the vehicle interior.
Hood seals: These seals are used to provide a tight seal between the hood and the vehicle body to prevent water, dust, and other contaminants from entering the engine compartment.
Trunk seals: These seals are used to provide a tight seal around the perimeter of the trunk to prevent water, dust, and noise from entering the vehicle interior.
When selecting automotive rubber seals, it’s important to choose a material that is compatible with the specific application and the environment in which the vehicle will be operating. For example, EPDM rubber seals are commonly used for outdoor applications because they are resistant to UV radiation and ozone. Neoprene rubber seals are commonly used for applications that require resistance to oil and chemicals. Silicone rubber seals are commonly used for applications that require resistance to high temperatures.
Overall, automotive rubber seals play an important role in preventing the ingress of water, dust, and other contaminants into the interior of vehicles, Automotive Rubber Seals and selecting the right type of seal for your application is critical for ensuring optimal performance and longevity.
How do I choose the right type of seal for my application?
Choosing the right type of seal for your application is important for ensuring optimal performance and longevity.
Here are some factors to consider when selecting the right type of seal:
Material compatibility: The seal material should be compatible with the fluid, temperature, and operating conditions of your application. For example, if the seal will be exposed to high temperatures, a silicone seal may be the best choice.
Size and shape: The seal should be the correct size and shape to provide a tight seal around the component it is sealing.
Environmental factors: Consider any environmental factors that may affect the seal, such as exposure to UV radiation, ozone, or chemicals.
Performance requirements: Consider the performance requirements of your application, such as the required level of sealing performance, durability, and resistance to wear.
Regulatory requirements: Some applications may require seals that comply with specific regulatory standards, such as those set by the FDA for food and beverage applications.
Cost considerations: Consider the cost of the seal and whether it fits within your budget.
It’s also important to choose a reputable seal manufacturer that provides high-quality products and reliable technical support. By considering these factors and working with a trusted manufacturer, you can select the right type of seal for your application and ensure optimal performance and longevity.
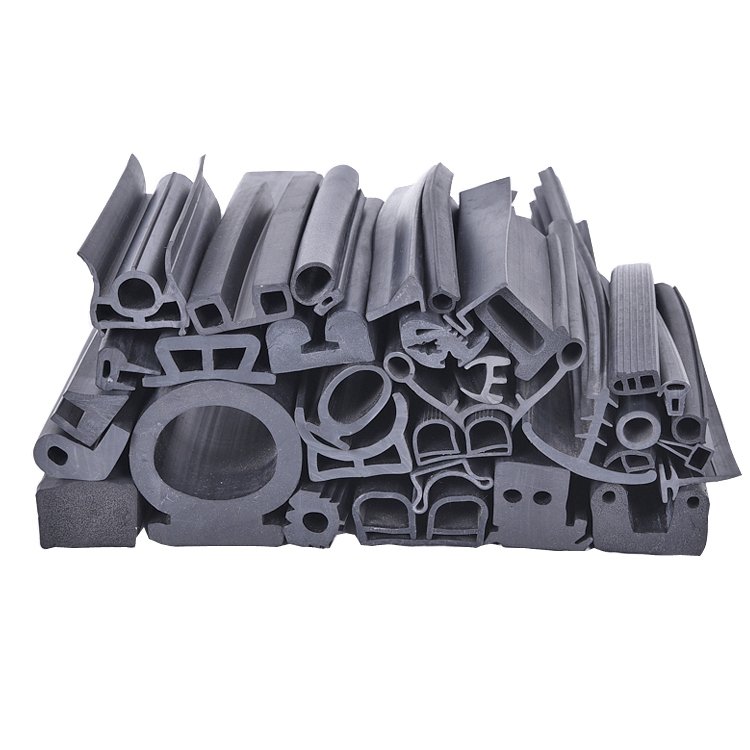